Trusted how to size a generator set for a factory Supplier
In today's competitive industrial landscape, uninterrupted power is not a luxury—it's a fundamental requirement for operational continuity, safety, and profitability. A sudden power outage can halt production lines, corrupt data, damage sensitive equipment, and lead to significant financial losses. A reliable standby generator set is the ultimate insurance policy against such disruptions. However, purchasing a generator is only half the battle. The most critical step is ensuring it is correctly sized for your facility's unique demands. An undersized generator will fail when you need it most, while an oversized one leads to unnecessary capital expenditure, higher fuel consumption, and potential engine damage from under-loading. This guide provides a detailed methodology for how to size a generator set for a factory, empowering you to make an informed and cost-effective decision.
Why Accurate Generator Sizing is Critical for Your Factory's Success
The process of sizing a generator, also known as a "genset," goes far beyond simply looking at your utility bill. It involves a meticulous analysis of your factory's entire electrical ecosystem. The consequences of improper sizing can be severe and far-reaching, impacting everything from your bottom line to your operational safety.
The Dangers of Undersizing:
- System Failure: The most obvious risk. When demand exceeds the generator's capacity, its circuit breaker will trip, shutting down power and defeating its entire purpose. This is especially dangerous during a utility outage.
- Equipment Damage: An overloaded generator can produce unstable voltage (voltage droop) and frequency, which can severely damage sensitive electronics, motors, and control systems connected to it.
- Reduced Generator Lifespan: Constantly running a generator at or above its maximum rated load causes excessive heat and stress on its components, leading to premature wear and a significantly shorter operational life.
The Problems with Oversizing:
- Higher Initial Cost: A larger generator comes with a bigger price tag, not just for the unit itself but also for installation, wiring, and potentially a larger footprint.
- Increased Fuel and Maintenance Costs: A bigger engine consumes more fuel, even at partial loads. Furthermore, running a diesel generator on a light load for extended periods can lead to a condition called "wet stacking," where unburned fuel and soot build up in the exhaust system, requiring costly maintenance and reducing efficiency.
- Reduced Efficiency: Generators are designed to operate most efficiently between 70-90% of their rated load. An oversized generator operating at a low load factor (e.g., 30%) wastes a significant amount of fuel.
Understanding the difference between kilowatts (kW) and kilovolt-amperes (kVA) is also crucial. kW represents the "real power" that performs actual work, like lighting a bulb or turning a motor. kVA represents the "apparent power," which is the total power consumed by the system, including both real power and reactive power (power required by inductive loads like motors). The relationship is defined by the Power Factor (PF): kW = kVA x PF. Factories with many motors typically have a lower power factor (e.g., 0.8), so you must size the generator based on the total kVA requirement.
Step-by-Step Process: How to Size a Generator Set for a Factory
To accurately determine the right generator size, you need to conduct a thorough load analysis. This methodical approach ensures no critical loads are missed and that all power characteristics are accounted for. Here is the professional step-by-step process for how to size a generator set for a factory.
Step 1: List All Electrical Loads
Begin by creating a comprehensive inventory of every single piece of equipment and lighting that needs to be powered by the generator. It's essential to decide whether you need to power the entire facility (full backup) or only essential systems (partial backup). For a partial backup, categorize equipment into "essential" and "non-essential."
Your list should include:
- Lighting: All indoor and outdoor lights.
- HVAC Systems: Air conditioners, heaters, ventilation fans, and chillers.
- Motors: Conveyor belts, pumps, compressors, machine tools (lathes, CNC machines), and fans.
- Office Equipment: Computers, servers, printers, and communication systems.
- Safety Systems: Emergency lighting, fire alarm systems, and security cameras.
- Specialized Machinery: Welding equipment, industrial ovens, and processing machinery.
Step 2: Determine Starting and Running Wattage
Every piece of equipment has two power ratings: running (or rated) watts and starting (or surge) watts. Running watts is the power consumed during normal operation. Starting watts is the extra power required to start the equipment, which can be 3 to 7 times higher than the running watts, especially for equipment with electric motors. This is known as inrush current.
You can find this information on the equipment's nameplate, in the owner's manual, or by contacting the manufacturer. If you cannot find the starting wattage, a general rule of thumb is to multiply the running wattage by 3 for motor-driven equipment. The generator must have enough capacity to handle the sum of all running loads plus the single largest starting load that will come online.
Step 3: Calculate Total Power Requirements
Once you have your list, you can calculate the total power needed.
- Sum the Running Watts: Add up the running watts of all the equipment that will operate simultaneously. This gives you your total running load in watts.
- Identify the Largest Starting Wattage: Find the single piece of equipment with the highest starting wattage from your list.
- Calculate Peak Demand: Add the largest starting wattage to your total running load. This result is a good estimate of the minimum generator capacity required. Formula: Total Watts = (Sum of all Running Watts) + (Highest Starting Watts).
- Convert to kVA: Since industrial generators are rated in kVA, you must convert your total watts (kW) to kVA. Divide your total kW by your factory's estimated power factor (typically 0.8 for industrial facilities). Formula: kVA = kW / 0.8.
Step 4: Account for Future Growth
A common mistake is sizing a generator only for current needs. Factories evolve, and you may add new machinery or expand your production lines in the future. It is a prudent and cost-effective strategy to plan for this growth. A standard industry practice is to add a capacity buffer of 20-25% to your calculated total kVA. This ensures your investment remains viable for years to come and prevents you from having to replace the generator prematurely.
Understanding Key Technical Specifications and Generator Types
Beyond pure size, several other technical factors influence the right generator choice for your factory. As a leading supplier, we help our clients navigate these specifications to find the perfect match for their operational environment.
Prime vs. Standby Power Ratings
Generators have different power ratings based on their intended use:
- Standby Power: This is the maximum power a generator can supply for a limited number of hours during a utility power outage. These generators are not intended for continuous use. This is the most common type for factory backup power.
- Prime Power: This rating is for generators that serve as the primary power source, such as in remote locations without utility access. They are designed to run for unlimited hours at a variable load.
- Continuous Power: This is for generators that run continuously at a constant load, 24/7. This is less common for factory applications unless they are co-generation plants.
For most factories, a generator with a Standby rating is the appropriate and most cost-effective choice.
Fuel Types: Diesel, Natural Gas, and Propane
The choice of fuel is a critical decision based on availability, cost, storage, and maintenance.
- Diesel: The most common choice for industrial standby generators. Diesel engines are robust, responsive, and fuel-efficient. Diesel fuel is stable and readily available, and on-site storage in large tanks is straightforward. They offer the best power density.
- Natural Gas: A growing preference for its environmental benefits and lower operating costs. If your factory has a reliable natural gas line, it eliminates the need for on-site fuel storage and refueling. However, they may have a higher initial cost and are dependent on the gas utility's integrity during a widespread disaster.
- Propane: Offers a long shelf life and clean-burning properties. Propane is stored on-site in tanks, similar to diesel, but may be more expensive and less energy-dense, requiring larger storage volumes.
Single-Phase vs. Three-Phase Power
Small residential or commercial buildings often use single-phase power. However, factories almost exclusively require three-phase power. Industrial machinery, large motors, and heavy-duty equipment are designed to run on three-phase power because it is more efficient and provides a more consistent power delivery, which is crucial for smooth motor operation.
The Automatic Transfer Switch (ATS)
An Automatic Transfer Switch (ATS) is a non-negotiable component for any factory backup power system. This intelligent device monitors the incoming utility power. When it detects an outage or instability, it automatically disconnects the facility from the utility grid and signals the generator to start. Once the generator is at operating speed, the ATS switches the factory's electrical load to the generator. When utility power is restored, the ATS switches the load back and signals the generator to shut down. This ensures a seamless, safe, and rapid transition to backup power with minimal human intervention.
Common Pitfalls to Avoid When Sizing Your Industrial Generator
Even with a guide, the complexities of industrial power systems can lead to costly errors. Being aware of these common pitfalls can save you significant time, money, and frustration.
- Ignoring Non-Linear Loads: Modern factories are filled with non-linear loads like variable frequency drives (VFDs), computer servers, and LED lighting. These can create harmonic distortion in the electrical system, which can cause overheating and control issues. Your generator must be properly sized and equipped with an alternator capable of handling these harmonics.
- Forgetting Derating Factors: A generator's power output is rated for specific environmental conditions (e.g., sea level and 25°C). If your factory is at a high altitude or operates in a high-temperature environment, the generator's output will be reduced, or "derated." You must account for these factors to ensure the generator can deliver the required power under your specific site conditions.
- Focusing Solely on Price: While budget is always a consideration, choosing the cheapest generator available is a false economy. Reliability, fuel efficiency, build quality, and the manufacturer's reputation are far more important. A premium-quality generator will provide reliable power for decades, while a low-cost, low-quality unit can become a constant source of maintenance headaches and may fail when needed.
- Neglecting Installation and Maintenance Logistics: Consider where the generator will be placed. Does it need a weatherproof and sound-attenuating enclosure? Is there proper ventilation? Do you have a plan for regular maintenance, including load bank testing, to keep it in peak condition? A reliable supplier will assist with these crucial planning stages.
Partnering with an Expert Supplier for Your Generator Needs
While this guide provides a robust framework, the most reliable way to ensure your factory is protected is to partner with an experienced and reputable generator supplier. The process of how to size a generator set for a factory is both an art and a science, requiring deep technical expertise and practical field experience. Our company is more than just a equipment provider; we are a comprehensive power solutions partner.
We welcome all inquiries, from large-scale industrial projects to individual business purchases. Our team of power systems engineers offers a consultative approach. We will work with you to conduct a professional on-site load analysis, considering every nuance of your operation. We provide detailed calculations and transparent recommendations, explaining the pros and cons of various options.
Our capabilities include:
- Wholesale and Retail Supply: We cater to both large industrial contractors and individual factory owners with flexible MOQs.
- Customization Options: We can provide generators with custom enclosures for sound attenuation and weather protection, oversized fuel tanks for extended run times, and advanced control panels for remote monitoring.
- Unwavering Commitment to Quality: All our generator sets are sourced from world-class manufacturers and undergo rigorous quality control checks and load testing before shipment. They are built to meet or exceed industry standards like ISO 9001.
- Comprehensive After-Sales Support: Our relationship doesn't end with the sale. We offer guidance on installation, commissioning, and developing a preventative maintenance schedule to ensure your generator provides reliable service for its entire lifespan.
Investing in the right-sized generator is one of the most important decisions a factory owner can make. Don't leave it to guesswork. Let our experts guide you through the process, ensuring your facility is equipped with a dependable, efficient, and perfectly sized power solution. Contact us today to discuss your factory's power requirements.
For more detailed information, please visit our official website:factory generator sizing
About the author: David Chen is a Senior Power Systems Engineer with over 15 years of experience specializing in industrial power generation and distribution. He has designed and commissioned backup power solutions for hundreds of manufacturing facilities, data centers, and critical infrastructure projects. David is passionate about helping businesses achieve operational resilience through meticulously planned and flawlessly executed power systems, ensuring they remain productive and secure no matter the circumstances. ---
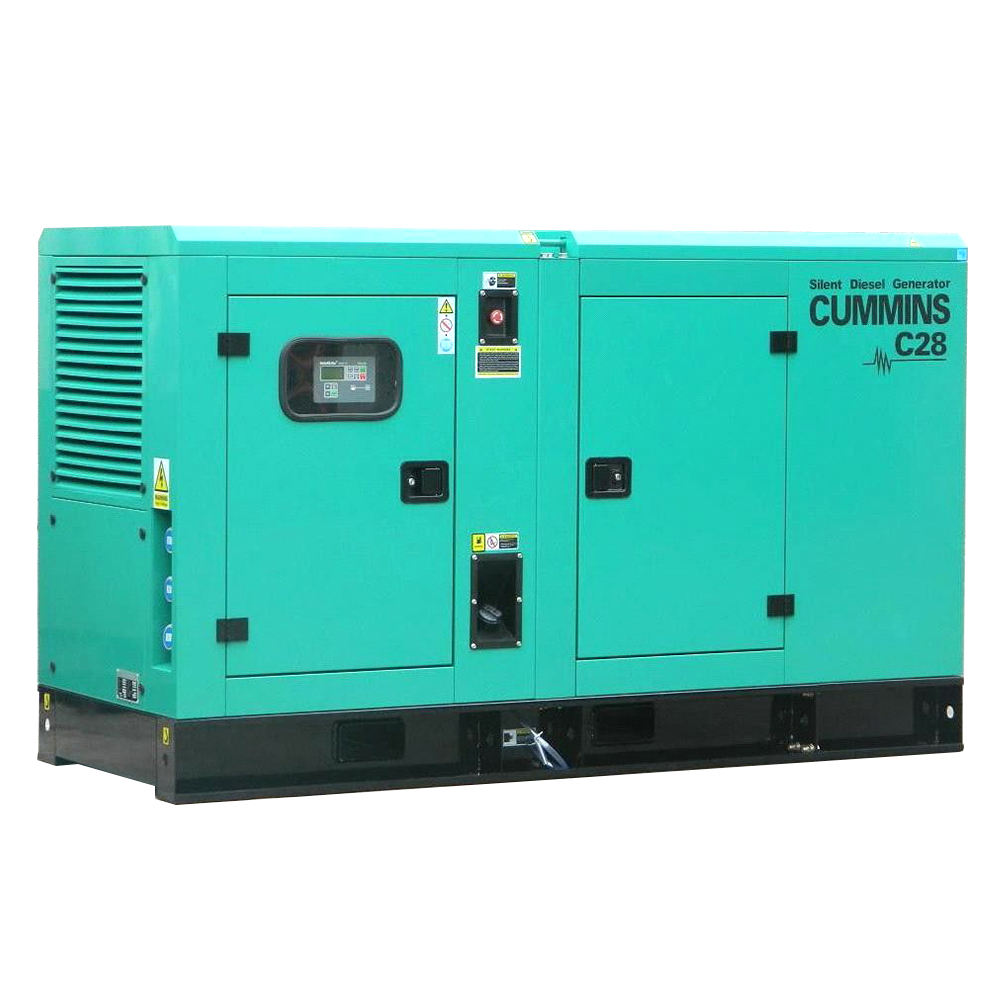
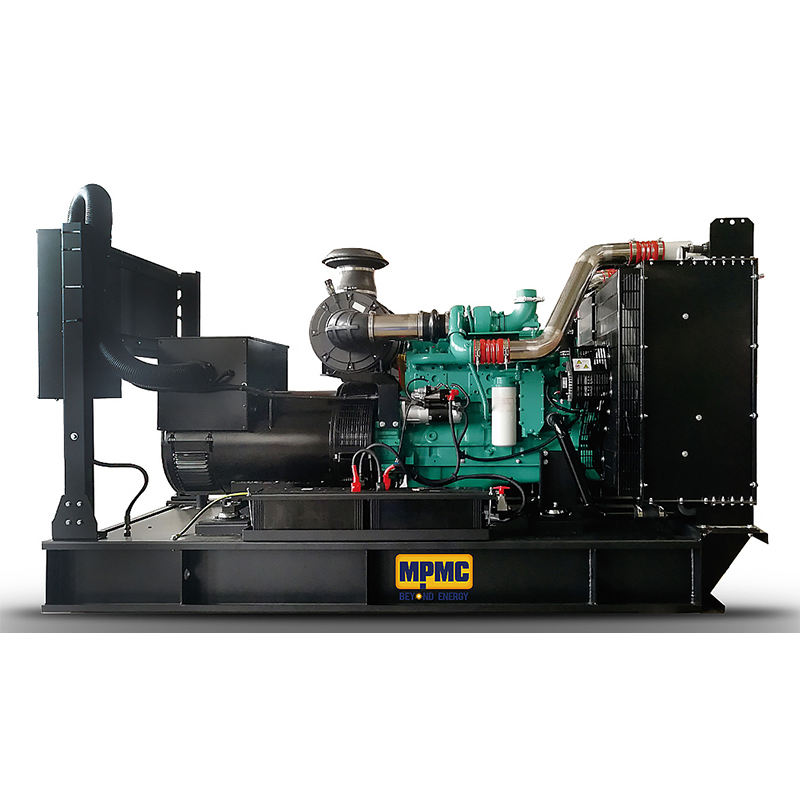
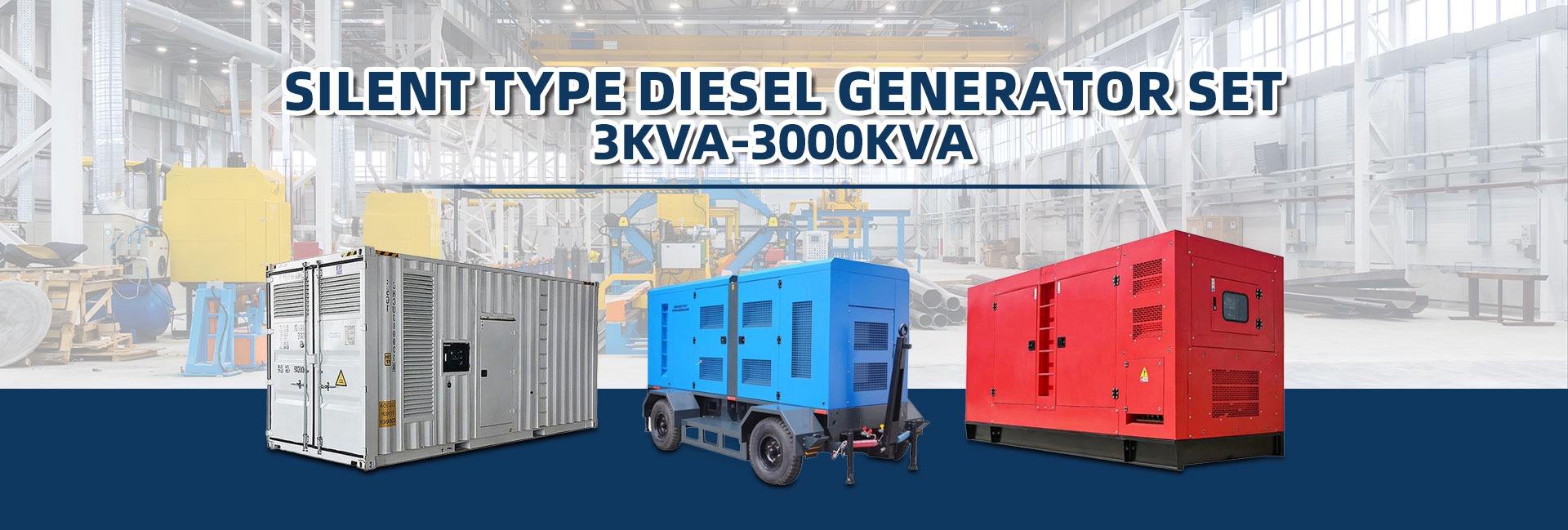