Power Outage Headaches? An Engineer\'s Guide to Ensuring Uninterrupted Industrial Operations
To be honest, few things can bring an industrial operation to a screeching halt faster than an unexpected power outage. The immediate impact is obvious: production stops, machinery goes idle, and critical processes are interrupted. But the true cost, the lingering "power outage headaches" that haunt plant managers and engineers, extends far beyond the momentary blackout. We’re talking about lost revenue, damaged equipment, safety hazards, spoiled raw materials, and perhaps most critically, a significant blow to reputation and customer trust. In today's hyper-competitive global landscape, where uptime is paramount, ensuring uninterrupted industrial operations isn't just a luxury; it's a fundamental necessity.
As engineers, we understand the intricate dance between power supply and operational continuity. Our role isn't merely to react to failures but to proactively design, implement, and maintain systems that are resilient, robust, and capable of weathering unforeseen disruptions. This guide is crafted from that engineering perspective, offering practical insights and actionable strategies to transform those potential power outage headaches into a well-managed, resilient power infrastructure. Ready to dive into the nuts and bolts of achieving true operational continuity?
Understanding the True Cost of Power Outage Headaches in Industrial Operations
Before we delve into solutions, it’s crucial to fully grasp the multifaceted impact of power interruptions. It's not just about the lights going out. For an industrial facility, every minute of downtime translates directly into tangible and intangible losses. From a tangible perspective, consider the immediate cessation of production lines, leading to missed deadlines and contractual penalties. Then there's the potential for equipment damage; sudden power loss can cause motors to seize, PLCs to corrupt data, or sensitive electronics to fail, necessitating costly repairs or replacements. Furthermore, in industries dealing with temperature-sensitive materials, chemicals, or perishable goods, an outage can lead to significant spoilage and waste, creating substantial financial write-offs.
Interestingly enough, the intangible costs often prove to be even more damaging in the long run. A reputation for unreliability can deter new clients and erode the trust of existing ones. Employee morale can suffer if they constantly face the frustration of interrupted work and the pressure of catching up. And let’s not forget the potential safety implications; critical safety systems, ventilation, or emergency lighting can be compromised, putting personnel at risk. Many experts agree that a comprehensive understanding of these costs is the first step towards justifying the necessary investments in power resilience. It's worth noting that a single major outage can easily cost an industrial facility hundreds of thousands, if not millions, of dollars, making the investment in prevention a clear economic imperative.
Proactive Engineering Strategies to Mitigate Power Outage Risks
The best defense against power outage headaches is a strong offense. This means adopting a proactive engineering mindset, focusing on identifying vulnerabilities and implementing preventative measures long before a crisis hits. In my experience, this phase is where the most significant long-term gains in reliability are made.
Power System Audits and Vulnerability Assessments
The starting point for any robust power strategy is a thorough audit of your existing electrical infrastructure. This isn't just about checking if the wires are connected; it involves a deep dive into your entire power distribution network. Engineers conduct detailed analyses of single points of failure, aging equipment, overloaded circuits, and potential bottlenecks. We look at everything from the utility service entrance to the last motor on the production floor. A comprehensive vulnerability assessment will identify weak links that could lead to an outage or exacerbate its effects. This often includes thermal imaging to detect hot spots, power quality analysis to identify harmonics or voltage sags, and insulation resistance testing.
Load Analysis and Capacity Planning
Understanding your facility's power consumption patterns is critical. Load analysis involves measuring and documenting the power requirements of all critical equipment under various operating conditions. This data is then used for meticulous capacity planning, ensuring that your current infrastructure can handle peak loads without strain and that future expansions are adequately supported. Overloading circuits is a common cause of trips and failures, and proper planning helps avoid these preventable power outage headaches. It also informs the sizing of backup systems, ensuring they are neither undersized (leading to failure) nor oversized (leading to unnecessary capital expenditure).
Redundancy and Diversification
Building redundancy into your power system is a cornerstone of uninterrupted operations. This means having backup systems or alternative pathways for power delivery. This could involve dual utility feeds from different substations, redundant transformers, or parallel busbar systems. Diversifying your power sources, where feasible, also adds another layer of resilience. For instance, combining grid power with on-site generation (like solar or co-generation) can significantly reduce reliance on a single point of failure. The goal here is to create a system where the failure of one component does not cascade into a complete system shutdown.
Implementing Advanced Solutions for Uninterrupted Industrial Operations During Power Outages
Once vulnerabilities are identified and planned for, the next step is to implement the physical and logical solutions that will keep your operations running when the grid falters. This is where the "engineer's guide" truly comes into play, focusing on proven technologies and smart integration.
Uninterruptible Power Supplies (UPS) and Battery Storage
For critical loads that cannot tolerate even a momentary interruption, Uninterruptible Power Supplies (UPS) are indispensable. These systems provide instantaneous backup power, typically from batteries, bridging the gap until generators can start up or grid power is restored. UPS systems come in various topologies (online, line-interactive, standby), each offering different levels of protection and efficiency. Selecting the right UPS for specific loads, considering factors like power quality, runtime requirements, and scalability, is a detailed engineering task. Modern battery technologies, including lithium-ion, are also offering more compact, efficient, and longer-lasting storage solutions, making them increasingly attractive for industrial applications.
Generator Systems (Diesel, Natural Gas)
For extended power outages, generator systems are the workhorses of industrial continuity. Diesel generators have long been the standard due to their reliability and readily available fuel. However, natural gas generators are gaining popularity due to lower emissions, quieter operation, and the potential for continuous fuel supply via pipeline. Sizing generators correctly is crucial, accounting for both continuous load and transient loads (like motor starting). Proper fuel management, ventilation, and exhaust systems are also key engineering considerations. Many facilities opt for multiple smaller generators operating in parallel for redundancy and scalability, rather than a single large unit.
Automatic Transfer Switches (ATS) and Seamless Transition
The bridge between utility power and backup power is the Automatic Transfer Switch (ATS). This device automatically senses a utility outage and signals the generator to start. Once the generator is stable, the ATS seamlessly transfers the load from the utility to the generator. When utility power returns, the ATS transfers the load back and signals the generator to shut down. The speed and reliability of this transfer are paramount for sensitive industrial equipment. Advanced ATS units can perform closed-transition transfers, where the load is momentarily paralleled between sources, ensuring virtually no interruption. This seamless transition is critical to preventing the very "power outage headaches" we aim to eliminate.
Renewable Energy Integration and Microgrids
Looking ahead, integrating renewable energy sources like solar PV or wind into an industrial facility's power strategy offers both sustainability benefits and enhanced resilience. When combined with battery storage and intelligent controls, these systems can form a "microgrid" – an independent energy system capable of disconnecting from the main grid and operating autonomously during an outage. This "islanding" capability provides a powerful layer of protection against grid instability. Designing and implementing microgrids requires sophisticated power electronics, energy management systems, and a deep understanding of grid synchronization and control, but the benefits in terms of energy independence and uninterrupted operations are substantial.
Sustaining Uninterrupted Industrial Operations Through Vigilant Monitoring and Maintenance
Installing state-of-the-art equipment is only half the battle. To truly ensure uninterrupted industrial operations, a commitment to ongoing monitoring, preventive maintenance, and continuous improvement is essential. This is where the engineer's work truly never ends.
Real-time Monitoring and SCADA Systems
Modern industrial facilities leverage Supervisory Control and Data Acquisition (SCADA) systems and other real-time monitoring platforms to keep a constant eye on their power infrastructure. These systems provide immediate alerts for anomalies like voltage fluctuations, current imbalances, temperature excursions, or equipment malfunctions. They allow engineers to remotely monitor the health of UPS units, generators, transfer switches, and even individual circuits. Early detection of issues can prevent minor problems from escalating into major power outage headaches. Data analytics from these systems can also reveal trends, predict potential failures, and optimize energy consumption.
Preventive and Predictive Maintenance Regimes
A robust maintenance program is non-negotiable. Preventive maintenance involves scheduled inspections, testing, and servicing of all power system components – checking battery health, exercising generators, cleaning electrical panels, and calibrating sensors. Predictive maintenance takes this a step further, using data from monitoring systems (e.g., vibration analysis, thermal imaging, oil analysis) to anticipate equipment failures before they occur. This allows for proactive repairs or replacements during planned downtime, avoiding costly emergency interventions and unexpected outages. In my experience, a well-executed predictive maintenance program can extend equipment life and significantly reduce unscheduled downtime.
Emergency Response Planning and Drills
Even with the most robust systems, unforeseen events can occur. A well-defined emergency response plan is crucial. This plan outlines clear procedures for personnel to follow during a power outage, including safety protocols, equipment shutdown sequences, manual transfer procedures (if applicable), and communication strategies. Regular drills are vital to ensure that personnel are familiar with these procedures and can execute them efficiently under pressure. This preparedness minimizes panic and helps to restore operations as quickly and safely as possible, mitigating the severity of any power outage headaches.
Empowering Your Team: The Human Factor in Preventing Power Outage Headaches
While technology forms the backbone of uninterrupted operations, the human element is equally critical. Skilled, knowledgeable, and well-trained personnel are indispensable for managing complex power systems and responding effectively to incidents.
Training and Certification
Investing in comprehensive training for your engineering and maintenance teams is paramount. This includes training on the specific power systems installed, safety procedures, troubleshooting techniques, and emergency protocols. Certifications in electrical safety, generator operation, and UPS maintenance ensure that your team possesses the necessary expertise. A well-trained team can identify subtle signs of potential failure, perform routine maintenance correctly, and respond decisively during an actual outage, thereby preventing minor issues from escalating into major power outage headaches.
Establishing Clear Protocols
Beyond individual training, establishing clear, unambiguous operational protocols and standard operating procedures (SOPs) for all power-related tasks is vital. This ensures consistency, reduces the likelihood of human error, and provides a framework for effective incident response. From routine checks to emergency shutdowns, documented procedures empower your team to act confidently and correctly, contributing significantly to the overall reliability of your industrial operations.
Embracing Innovation for Future-Proofing Industrial Operations Against Power Outages
The landscape of power generation and distribution is constantly evolving. As engineers, it's our responsibility to stay abreast of emerging technologies and innovations that can further enhance the resilience and efficiency of industrial power systems.
Smart Grid Integration
The concept of the "smart grid" is transforming how power is delivered and consumed. For industrial facilities, integrating with smart grid technologies can offer benefits like demand response programs, where facilities can reduce consumption during peak times in exchange for incentives, or even sell excess power back to the grid. This integration also provides more granular data on grid health, allowing for better anticipation of potential disruptions. While still evolving, smart grid integration holds promise for a more resilient and interactive power ecosystem.
IoT and AI for Predictive Analytics
The Internet of Things (IoT) is revolutionizing industrial maintenance. By embedding sensors into power equipment, engineers can collect vast amounts of real-time data on performance, temperature, vibration, and more. Artificial intelligence (AI) and machine learning algorithms can then analyze this data to identify patterns, predict equipment failures with remarkable accuracy, and optimize maintenance schedules. This shift from reactive to truly predictive maintenance is a game-changer in preventing power outage headaches, allowing facilities to address issues before they ever impact operations.
The Engineer's Ongoing Commitment to Eliminating Power Outage Headaches
Ensuring uninterrupted industrial operations is not a one-time project; it's an ongoing commitment, a continuous cycle of assessment, implementation, monitoring, and improvement. The "power outage headaches" that once plagued industrial facilities can indeed be mitigated, if not entirely eliminated, through a diligent and strategic engineering approach. From proactive risk assessments and the implementation of robust backup solutions to vigilant monitoring, comprehensive maintenance, and empowering your workforce, every step contributes to a more resilient and reliable operation.
As technology advances and energy landscapes shift, the role of the engineer in safeguarding industrial continuity becomes even more critical. By embracing innovation and applying sound engineering principles, we can ensure that industrial operations remain productive, safe, and profitable, regardless of what happens on the grid.
For more detailed information, please visit our official website:Power outage
About the author: John "Jack" Thompson is a seasoned electrical engineer with over two decades of experience designing and optimizing industrial power systems. Specializing in critical infrastructure and operational continuity, Jack has guided numerous facilities through complex power resilience projects, from initial vulnerability assessments to the implementation of advanced microgrid solutions. His passion lies in transforming potential power outage headaches into robust, reliable systems that ensure seamless industrial operations.
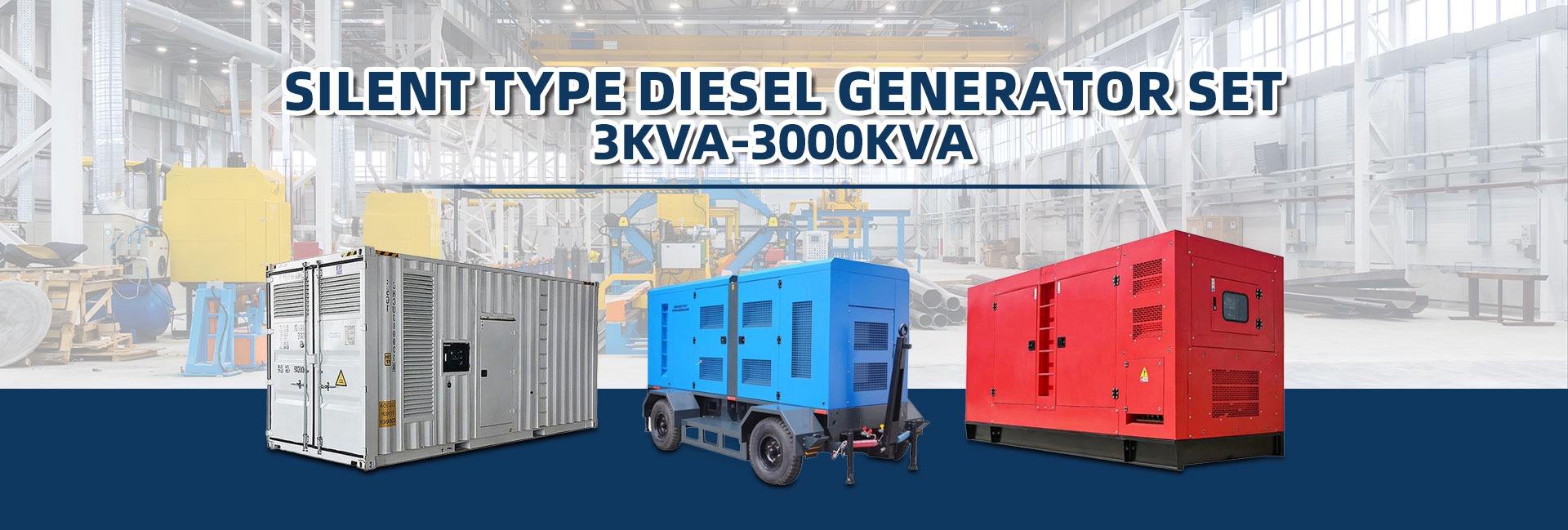
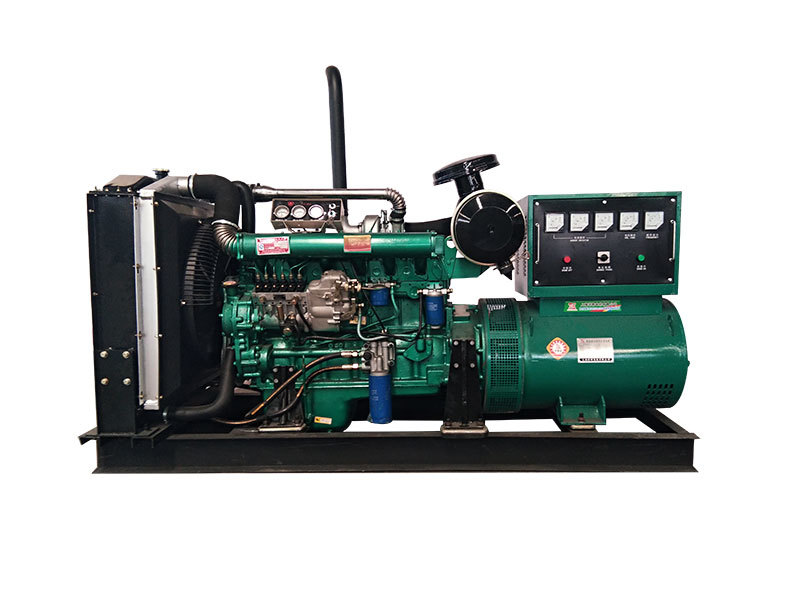
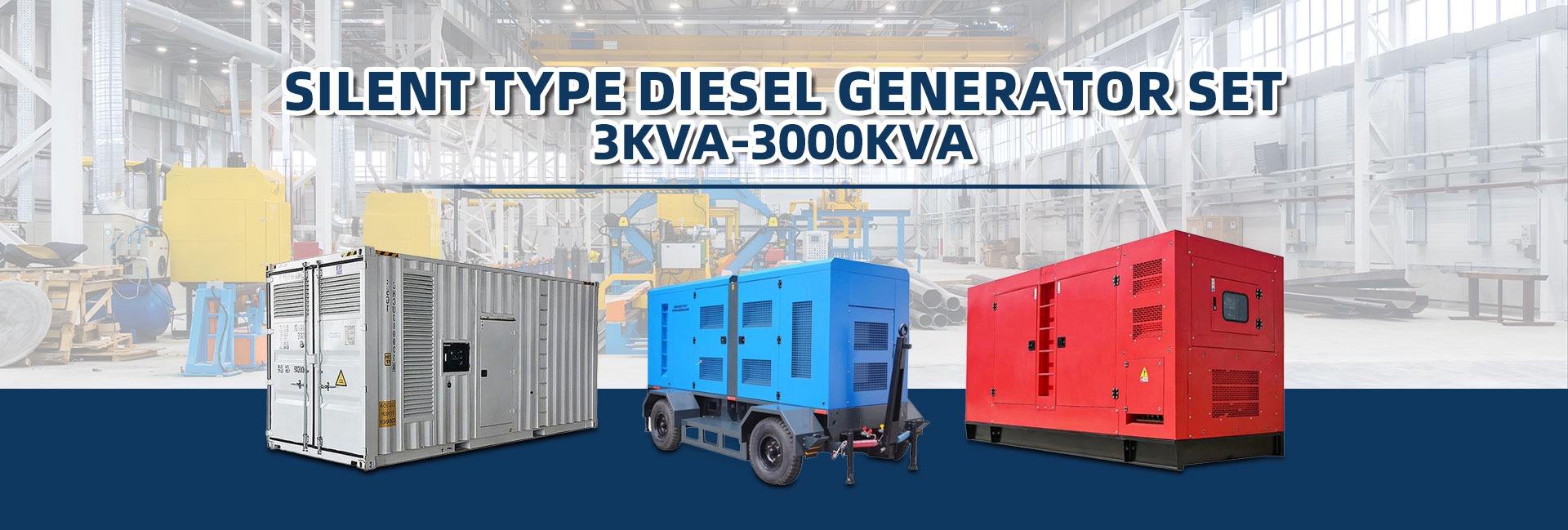