From Spec to Solution: Your Manufacturer\'s Insider Checklist for a Seamless Generator Set Project
Embarking on a generator set project, whether for backup power, prime power, or a complex grid-tie application, can feel like navigating a labyrinth. The journey from an initial concept or a pressing need (the "spec") to a fully operational, reliable power source (the "solution") involves myriad critical steps. As a manufacturer, we’ve witnessed firsthand the difference a meticulous, insider-guided approach makes. Our goal isn't just to sell you a generator; it's to partner with you to deliver a truly seamless power solution that performs flawlessly for decades. But how do you ensure that the solution truly aligns with your long-term operational goals and avoids costly pitfalls?
This article provides an insider's checklist, gleaned from years of experience, to help you understand the manufacturer's perspective and what truly goes into a successful project. It's about more than just horsepower and voltage; it's about a holistic approach that covers everything from the minutiae of site conditions to the nuances of post-installation support. Let's delve into the core elements of transforming your generator set specification into a robust, reliable solution.
Defining the Blueprint: The Criticality of Initial Specification in a Seamless Generator Set Project
The journey from spec to solution begins long before any metal is cut or wires are connected. It starts with a comprehensive and accurate specification. In my experience, this initial phase is arguably the most critical. A well-defined specification is the bedrock upon which a truly seamless generator set project is built. Without it, you’re essentially building a house without blueprints, leading to potential delays, cost overruns, and, ultimately, a solution that doesn't quite fit your needs.
Understanding Your Power Demands and Application
To be honest, many projects falter because the initial power requirements aren't fully understood or accurately assessed. It's not just about peak load; it's about understanding the load profile, transient response requirements, and the nature of the connected equipment. Are there significant motor starting loads? Is sensitive electronic equipment involved? What is the ambient temperature and altitude at the installation site? These factors directly impact the generator's sizing, cooling system, and overall performance.
- Load Profile Analysis: Detail all connected loads, including resistive, inductive, and capacitive components. Consider future expansion plans.
- Standby vs. Prime Power: Clearly define the application. Is it emergency backup, continuous operation, or peak shaving? This dictates duty cycle and design parameters.
- Environmental Conditions: Temperature, humidity, altitude, and even seismic activity can significantly affect generator performance and require specific modifications.
- Fuel Type and Storage: Diesel, natural gas, propane – each has implications for fuel storage, supply, and regulatory compliance.
Regulatory Compliance and Site Considerations
Interestingly enough, what often gets overlooked in the early stages are the regulatory and site-specific requirements. Emissions standards (e.g., EPA Tier, CARB), noise restrictions, local building codes, and even fire safety regulations vary significantly by location. Addressing these upfront saves immense headaches down the line.
- Emissions Regulations: Identify all applicable local, state, and federal emissions standards. This impacts engine selection and exhaust aftertreatment.
- Noise Attenuation: Is the generator located near residential areas or noise-sensitive zones? Acoustic enclosures or specialized baffling might be necessary.
- Footprint and Access: The physical dimensions of the generator, along with access for delivery, installation, and future maintenance, are crucial. Will it fit through existing doorways? Is there enough space for service personnel?
- Foundation and Structural Support: A generator set is heavy. The foundation must be capable of supporting its weight and absorbing vibrations.
This comprehensive approach to specification ensures that when we, as manufacturers, begin the design phase, we have a clear, accurate picture of your needs, paving the way for a truly seamless solution.
Collaborative Design & Engineering: Translating Spec into a Robust Generator Set Solution
Once the specification is meticulously defined, the next critical phase in achieving a seamless generator set project is the collaborative design and engineering process. This is where the "spec" truly begins its transformation into a tangible "solution." From a manufacturer's perspective, this isn't just about picking components off a shelf; it's about intricate system integration, custom adaptations, and ensuring every detail aligns with the project's unique demands. Many experts agree that effective communication between the client and the engineering team at this stage is paramount.
System Integration and Customization
It's worth noting that very few generator set projects are truly "off-the-shelf." Most require a degree of customization to integrate seamlessly into existing infrastructure or to meet specific operational requirements. Our engineering team utilizes advanced CAD and simulation tools to model the proposed solution, identifying potential conflicts or optimizations early on. This iterative process allows for fine-tuning before any physical manufacturing begins, significantly reducing the risk of costly rework later.
- Electrical Integration: Designing the switchgear, automatic transfer switches (ATS), paralleling controls, and protective relays to integrate flawlessly with your facility's electrical system.
- Mechanical Integration: Considering fuel lines, exhaust systems, cooling systems, and ventilation. Are there specific routing challenges? Does the exhaust need to be routed through multiple floors?
- Control System Design: Tailoring the generator control panel to your operational preferences, including remote monitoring capabilities, alarm notifications, and integration with building management systems (BMS).
- Specialized Enclosures: Beyond standard weather-resistant enclosures, custom solutions for extreme environments (e.g., desert, arctic), higher security, or specific aesthetic requirements are often designed.
Value Engineering and Future-Proofing
In my experience, a truly seamless solution isn't just about meeting current needs; it's about anticipating future ones. This is where value engineering comes into play. It’s not about cutting corners, but about optimizing the design to provide the best long-term value, considering factors like fuel efficiency, maintenance accessibility, and scalability. Are there opportunities to incorporate modular designs for easier future upgrades? Can we select components that have a proven track record of reliability and readily available spare parts?
- Component Selection: Choosing reputable, high-quality components (engine, alternator, controls) that offer longevity and performance.
- Maintenance Accessibility: Designing the layout to ensure easy access for routine service and major overhauls, reducing downtime and maintenance costs.
- Scalability: Planning for potential future power needs, perhaps by designing for paralleling capabilities or space for additional units.
- Cybersecurity for Controls: With increasing connectivity, ensuring the control system is robust against cyber threats is a growing consideration.
This phase is a true partnership. Your insights into your operational environment, combined with our engineering expertise, forge a design that is not only technically sound but also practically optimized for a seamless long-term solution.
Precision Manufacturing & Rigorous Quality Assurance: Building the Seamless Solution
With the design finalized, the project moves into the manufacturing phase – where the blueprint transforms into a physical asset. For a seamless generator set project, precision manufacturing coupled with rigorous quality assurance is non-negotiable. This isn't merely assembly; it's a meticulous process that ensures every component, every weld, and every connection meets the highest standards. From an insider's perspective, this is where our commitment to reliability truly shines, preventing issues before they ever leave our facility.
Strategic Sourcing and Component Integration
To be honest, the quality of the final product is only as good as the quality of its individual components. We place immense emphasis on strategic sourcing, partnering with trusted suppliers for engines, alternators, control systems, and other critical parts. This ensures consistency and reliability. Once components arrive, the integration process is carefully managed, often using lean manufacturing principles to optimize efficiency without compromising quality.
- Supplier Vetting: Rigorous evaluation of all component suppliers to ensure they meet our stringent quality and performance criteria.
- Inventory Management: Ensuring timely availability of all necessary parts to prevent production delays.
- Skilled Craftsmanship: Our manufacturing teams comprise highly trained technicians and engineers who specialize in generator set assembly, wiring, and fabrication.
- Modular Assembly: Utilizing modular construction where possible to enhance efficiency, quality control, and ease of future maintenance.
Multi-Stage Quality Control and Testing
Interestingly enough, the term "quality assurance" is often used broadly, but in our world, it means a multi-layered approach to inspection and testing at every stage of production. It's not just a final check; it's an ongoing process from the moment raw materials arrive until the generator is ready for shipment. This proactive approach is fundamental to delivering a truly seamless solution.
- Incoming Material Inspection: Verifying the quality and specifications of all raw materials and purchased components.
- In-Process Inspections: Regular checks during various assembly stages, such as wiring continuity, torque specifications, and fluid connections.
- Sub-Assembly Testing: Testing individual components or sub-assemblies (e.g., control panels, cooling systems) before final integration.
- Final Assembly Verification: A comprehensive checklist to ensure all components are correctly installed and connected.
This meticulous attention to detail during manufacturing is what allows us to confidently stand behind our products. It’s the behind-the-scenes work that ensures your generator set arrives ready to perform flawlessly.
Testing, Commissioning, and Installation Support: Ensuring a Seamless Transition to Solution
The journey from spec to solution doesn't end when the generator set rolls off the production line. In fact, some of the most critical steps for ensuring a truly seamless generator set project occur post-manufacturing, during testing, commissioning, and installation. This phase is about proving the solution's capabilities and integrating it flawlessly into your operational environment. Many experts agree that inadequate testing or commissioning can undermine even the best-designed and manufactured equipment.
Factory Acceptance Testing (FAT)
Before any generator set leaves our facility, it undergoes rigorous Factory Acceptance Testing (FAT). This is a crucial step that allows you, the client, to witness the generator's performance under simulated load conditions, verifying that it meets all specified requirements and operates as expected. It’s an opportunity to identify and address any potential issues in a controlled environment, preventing surprises during on-site commissioning.
- Load Bank Testing: Running the generator at various load percentages (e.g., 25%, 50%, 75%, 100%) for extended periods to verify stable voltage, frequency, and temperature.
- Transient Response Testing: Assessing the generator's ability to handle sudden load changes, crucial for sensitive equipment.
- Control System Verification: Testing all control panel functions, alarms, shutdowns, and remote monitoring capabilities.
- Safety Feature Checks: Ensuring all safety shutdowns and protective devices are fully functional.
- Client Witnessing: Encouraging clients to be present during FAT to personally verify performance and ask questions.
This comprehensive FAT process provides peace of mind, ensuring that the solution you receive has been thoroughly vetted and performs exactly as promised.
On-Site Installation and Commissioning (SAT)
Once the generator set arrives at your site, the focus shifts to installation and Site Acceptance Testing (SAT). While installation is often handled by a qualified contractor, our role as a manufacturer extends to providing detailed guidance and, often, on-site supervision or technical support. Commissioning is the final critical step, where the generator is integrated with your facility's systems and brought online.
- Installation Guidance: Providing detailed manuals, drawings, and, if necessary, on-site technical assistance to ensure correct installation.
- Pre-Commissioning Checks: Verifying all physical connections, fluid levels, and electrical wiring before startup.
- Site Acceptance Testing (SAT): Replicating key FAT tests on-site, verifying integration with ATS, paralleling gear, and facility loads. This confirms the entire system functions seamlessly in its operational environment.
- Operator Training: Providing comprehensive training for your personnel on the generator's operation, maintenance, and troubleshooting. This empowers your team to manage the solution effectively.
Isn't it true that the true measure of a seamless project is how well the solution integrates and performs in its real-world setting? Our commitment extends through this crucial phase, ensuring a smooth handover and operational readiness.
Long-Term Partnership: Post-Installation Support and Maintenance for a Truly Seamless Solution
A generator set project isn't truly seamless if the relationship ends at commissioning. For a manufacturer, delivering a solution means committing to its long-term performance and reliability. Post-installation support and proactive maintenance are essential components of ensuring your generator set continues to operate flawlessly for its entire lifespan, evolving from a mere piece of equipment into a dependable, enduring power solution. This is where the true value of partnering with a dedicated manufacturer becomes evident.
Proactive Maintenance and Service Programs
In my experience, the biggest factor in extending the life and reliability of a generator set is consistent, professional maintenance. Just like any complex machinery, generators require regular check-ups, fluid changes, and component inspections. We offer tailored service programs designed to keep your generator in peak condition, often preventing minor issues from escalating into major problems. It's about being proactive, not reactive.
- Preventive Maintenance Schedules: Offering various service plans based on operating hours, environmental conditions, and application, including routine inspections, fluid analysis, and filter changes.
- Remote Monitoring Solutions: Providing systems that allow for real-time monitoring of generator performance, fault codes, and operational data, enabling early detection of potential issues.
- Emergency Service and Support: Ensuring rapid response times for unexpected breakdowns, with qualified technicians available 24/7.
- Genuine Parts Availability: Maintaining a robust inventory of genuine spare parts to ensure quick repairs and optimal performance, as non-OEM parts can compromise reliability.
Technical Support and System Upgrades
Interestingly enough, technology evolves, and so do operational needs. A truly seamless solution anticipates this evolution. Our technical support team serves as a continuous resource, providing expert advice and troubleshooting assistance. Furthermore, we actively work with clients to identify opportunities for system upgrades or modernizations that can enhance performance, efficiency, or compliance over time.
- Dedicated Technical Support: Access to experienced engineers and technicians for troubleshooting, operational advice, and complex problem resolution.
- Software and Firmware Updates: Providing updates for control systems to enhance functionality, improve efficiency, or address security vulnerabilities.
- System Modernization: Advising on and implementing upgrades for older units, such as control panel modernizations, emissions compliance upgrades, or efficiency improvements.
- Training Refreshers: Offering ongoing training programs to ensure your staff remains proficient in operating and performing basic maintenance on the generator set.
This commitment to long-term partnership ensures that your investment continues to deliver reliable power, making the journey from spec to solution a truly continuous and seamless experience. It’s about building a relationship that lasts as long as your generator set does, providing peace of mind and unwavering support.
Navigating Challenges and Ensuring Project Success: An Insider's Perspective on Your Seamless Generator Set Project
While the goal is always a seamless generator set project, the reality is that complex endeavors can encounter unforeseen challenges. From an insider's perspective, anticipating these hurdles and having a robust strategy to overcome them is as crucial as the initial planning. Ensuring project success isn't just about avoiding problems; it's about effectively managing them when they arise, maintaining momentum from spec to solution.
Proactive Risk Management and Communication
To be honest, no project is entirely without risk. The key is identifying potential risks early and developing mitigation strategies. This involves transparent communication between all stakeholders – client, manufacturer, and contractors. Many experts agree that open dialogue is the most powerful tool in preventing minor issues from snowballing into major setbacks. We believe in being upfront about potential challenges and collaboratively finding solutions.
- Contingency Planning: Developing backup plans for potential delays in material sourcing, unexpected site conditions, or logistical challenges.
- Regular Progress Meetings: Scheduling consistent check-ins to review progress, discuss any emerging issues, and adjust timelines or resources as needed.
- Clear Documentation: Maintaining comprehensive records of all communications, design changes, and approvals to avoid misunderstandings.
- Stakeholder Alignment: Ensuring that all parties involved in the project – from your operational team to our engineers – are aligned on objectives and expectations.
Flexibility and Problem-Solving
Interestingly enough, the true test of a manufacturer's commitment to a seamless solution often comes when an unexpected challenge presents itself. Whether it's a last-minute change in site access or a newly introduced regulatory requirement, our ability to adapt and problem-solve creatively is paramount. We don't just build generators; we build solutions, and that includes navigating the complexities of real-world projects.
- Adaptive Design: Being able to make necessary design adjustments mid-project while minimizing impact on schedule and cost.
- Technical Expertise on Demand: Having a team of experts ready to provide swift technical solutions to unforeseen challenges.
- Logistical Agility: Managing shipping, customs, and on-site delivery with precision, especially for international or remote installations.
- Post-Installation Troubleshooting: Providing immediate and effective support if any issues arise during or after commissioning.
Ultimately, a seamless generator set project isn't just about the product itself, but about the entire ecosystem of support, expertise, and partnership that surrounds it. From the initial spec to the final, fully operational solution, our commitment is to guide you every step of the way, ensuring your power needs are met with unparalleled reliability and efficiency.
Choosing the right manufacturer is about more than just a purchase; it's about entering into a partnership that guarantees peace of mind and a robust power solution for years to come. Our insider checklist is designed to empower you with the knowledge to demand and achieve nothing less than a truly seamless project.
For more detailed information, please visit our official website:Generator set project
About the author: The author is a seasoned expert in industrial power generation, with over two decades of experience in manufacturing, engineering, and project management for generator sets. Specializing in bespoke power solutions, their insights are rooted in a deep understanding of client needs and the intricate processes required to deliver reliable, high-performance systems from initial concept to long-term operation.
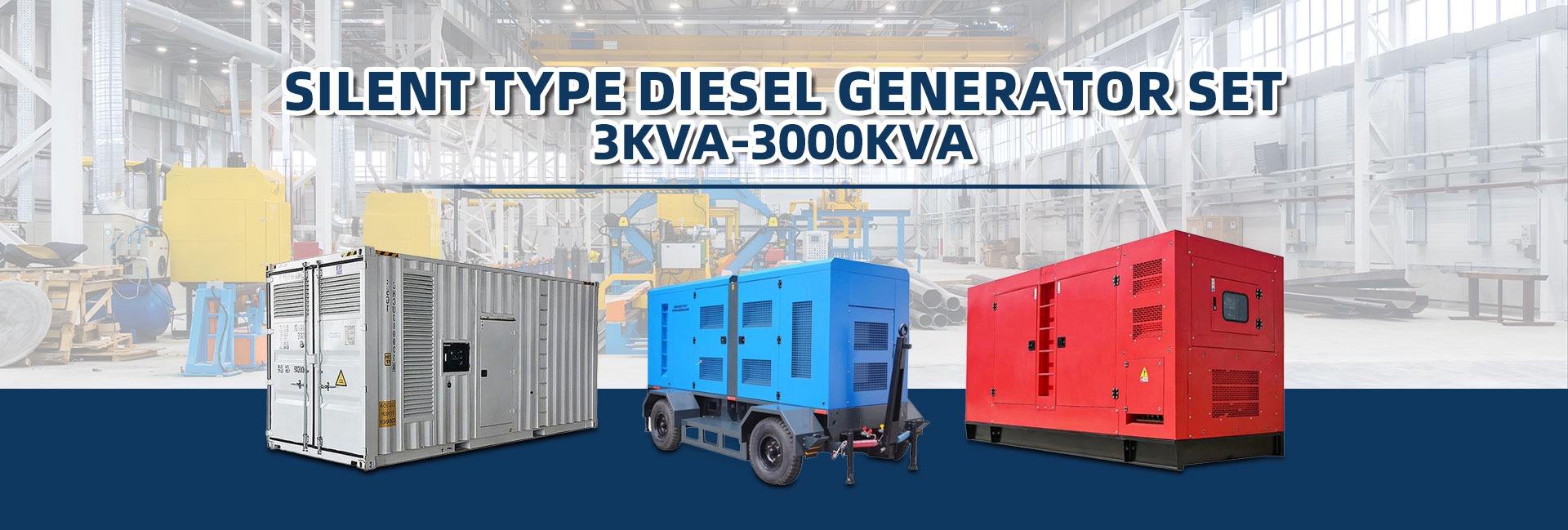
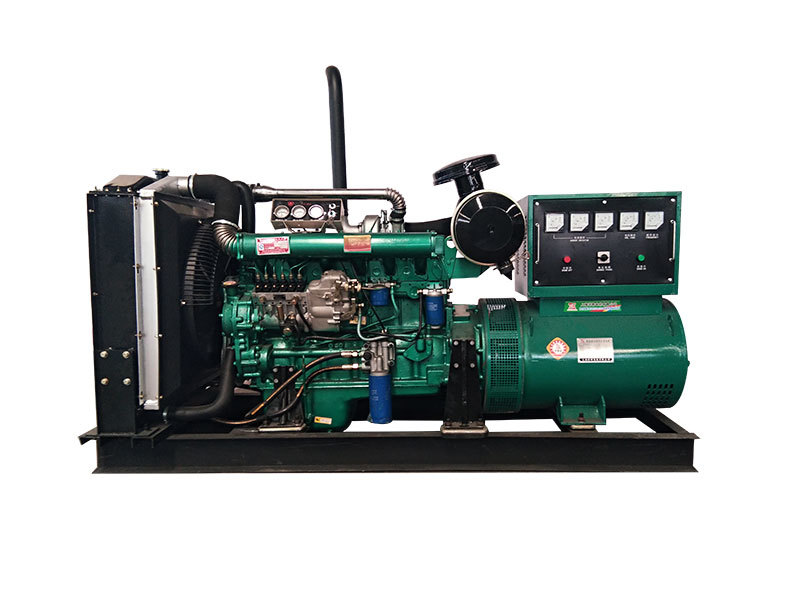
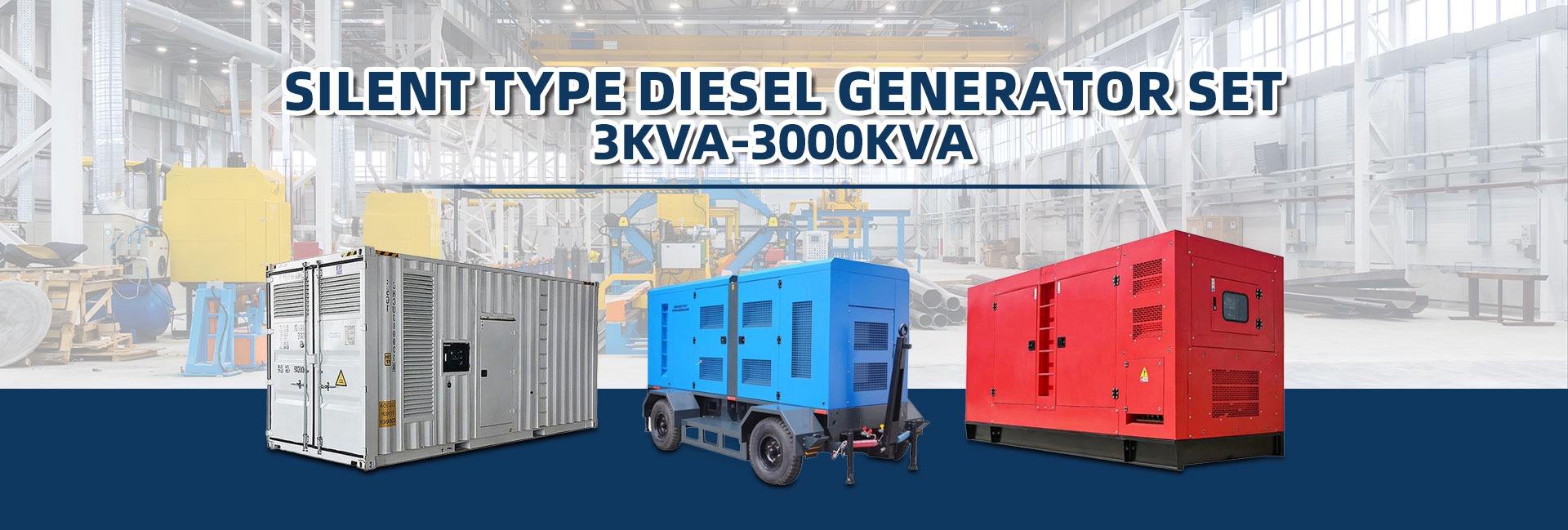